Part one: The manufacturing of customized RFID tag
With this article, Trace ID wants to offer the most complete guide about RFID tags in an online article, in a brief, clarifying way. Our purpose is that who is in need of the most complete information about RFID tags could find it here reunited in a unique article on the web. We consider it useful for all users interested in RFID technology, and in order to have this information updated and verified, we hope that the users don’t hesitate to contact us at info@trace-id.com.
The RFID technology
The acronym RFID means Radio Frequency Identification and named the system of collecting, storage and updating data through radio waves. The basic purpose of an RFID system is the distinctive traceability of objects, animals and humans, providing them with an individual number within the RFID tag they are attached with.
The RFID technology precedents go back to twenties, however, it wasn’t developed for civil use of industry and commerce with a global spread, up to only two decades ago. Perhaps, you could find interesting the history of the RFID start we have explained previously here.
What is an RFID system and what is it for?
The RFID system is the combination of several elements which storage, reproduce and update the information by interacting with each other. These elements are:
- An RFID tag.
- An RFID reader.
- A device for storage and manage data.
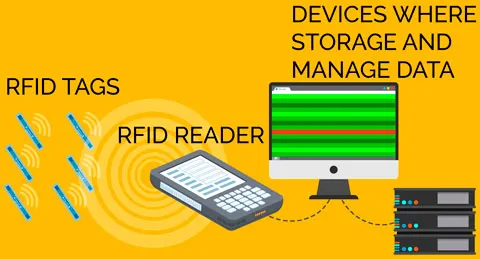
Basic concepts about RFID tags
Following, we are going to focus on the RFID tags properly speaking, and afterwards, we will detail the difference with customized RFID tags.
What is an RFID tag?
An RFID tag is an item formed by:
- An antenna.
- A radio transducer.
- A chip attached to the antenna by a resin that encapsulates it.
- A support substrate for these elements.
- Finally, an adhesive substance that makes possible that the tag could be affixed where it was necessary.
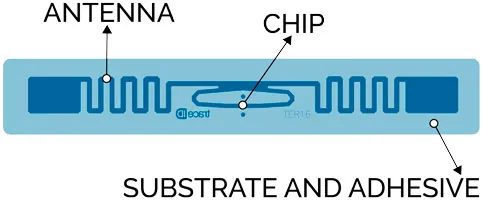
RFID tag frequencies
RFID frequency refers to the size of the radio waves used to communicate between RFID system components. The bigger is a wave the lower is the number of repetitions that a complete waveform can do within one second. 1Hz equals one wave in one second, 1KHz equals a thousand waves per second, and 1MHz equals one million waves per second. The kind of frequency determines some behaviours of the whole RFID system, for example, the lower is frequency the slower is the data read rate but it has higher capabilities for well reading near metals or liquids. On the other hand, the higher is the frequency the faster is the data read rate and the longer are the read ranges, but unfortunately, it has more sensitivity to interferences due to metals or fluids in the environment.
Low-frequency (LF RFID) covers from 125KHz to 134KHz and provides a read range of 10cm. High-frequency (HF RFID) usually operates at 13.56MHz and has read ranges from 10cm to 1m. Finally, Ultra high frequency (UHF RFID) covers 433MHz and from 860MHz to 960MHz. The read range of UHF systems can be as long as 12m, and it has a faster data transfer rate than LF or HF, but it’s the most sensitive to interference and it can’t read through metal or water.
How RFID tags are manufactured
The RFID antennas
To produce RFID tags, first, it’s made an antenna design based on an aim or needs that we want to solve. The antenna design could be created with various software. In Trace ID, our developer designs the antennas with Genesys, a specialized software of the latest generation. Later the antennas are designed we can already manufacture them.
The antennas that Trace ID commercializes are made of aluminium, but others could be made of copper, metallic tints, or even some are now being developed of carbon fibre.
The aluminium antennas are manufactured from bobbins of aluminium on PET that measure very few microns of thickness. A reserve that marks out the area of the antenna is applied on the aluminium in order to remove the surplus, so only the aluminium antenna shapes remain over the PET bobbin. Once the antennas bobbins are ready, they can pass to the next step for the antennas manufacturing.
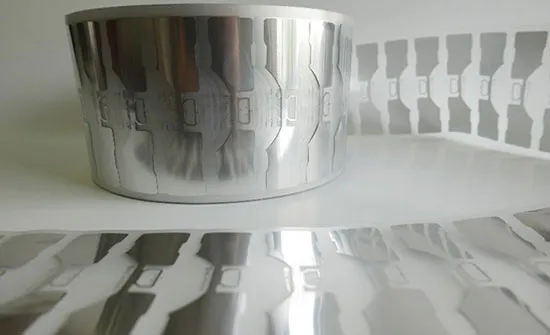
RFID chips
The RFID chips storage the information that is broadcasted through the radio waves thanks to the antenna and the RFID reader too. The chip is stimulated when receives a radiofrequency petition sent from a reader, and, in turn, broadcasts the data that itself contains.
This stimulation can be active or passive. An RFID tag is passive when it doesn’t bring a battery that produces the power needed for broadcasting back the information. So, the circuit is activated because by induction and the antenna takes up the most of the space in the RFID tag, because the antenna has the double function of receiving the power and broadcasting the radio signal with the data stored in the chip.
The Trace ID’s tags are equipped with the chips from the two leading providers in the RFID industry that are IMPINJ and NXP.
The bonding machines
The next step is the chip’s insertion in the antennas. This task is done in the bonding machines. There are various machines for manufacturing RFID technology, in Trace ID we are provided by the best manufacturers, in this case, the bonding and converting machines are from Mühlbauer.
The antennas bobbin enters to the bonding machine and the chips are attached in an exact point of each antenna in the bobbin by a resin called epoxide. When the bobbin gets out, it has become a bobbin of “dry inlays” this is how are named the antennas equipped with a chip.
The dry inlay
As we have already said, the dry inlay is the antenna equipped with a chip over a PET bobbin. It lacks adhesive and it doesn’t have the shape of a tag, so these dry inlays are no tags yet.
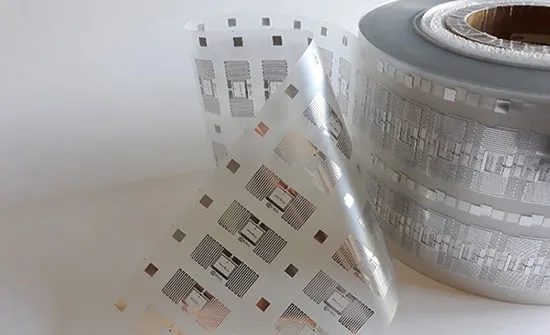
The converting machines
The converting machine is the machine where the dry inlays bobbin becomes a bobbin of “wet inlays”, that means that the bobbin no longer brings only dry inlays but it will bring the inlays cut as tags and it will have adhesive substance.
The manufacturing of the wet inlays
In this machine, the dry inlays that are over the PET layer will become covered by an adhesive substance over a layer of siliconized paper. Afterwards, they are cut according to the tag measure needed. The cutting affects all the layers except the siliconized paper. Finally, the surplus is removed and only the wet inlays remain over the siliconized paper with the shape of a tag. So, the wet inlays can already be taken off the siliconized paper and be stuck on over any surface like tags.
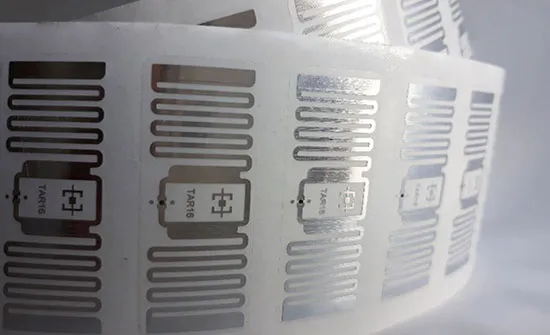
The manufacturing of the white wet inlays
The process of manufacturing the “white wet inlays” is the same as the wet inlays manufacturing but it is added to a layer of paper as a frontal face of the tag.
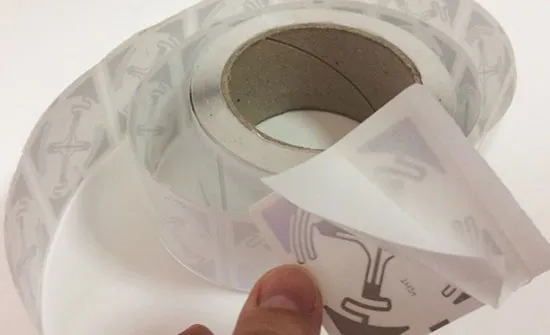
Customized RFID label formats
As we have previously said, the customized RFID label formats can vary a lot depending on the specific need of each RFID deployment. Even so, we can count the most common formats in the RFID industry.
- Sandwich: the RFID inlay is inserted between two sheets. These sheets hold the inlay and are usually printed with human reading information.
- Encapsulated: it is generally encapsulated to protect the inlay against fluids.
- On foam: the foam provides a necessary thickness to separate the inlay from for example metals. This is done because radiofrequency is affected especially by the presence of metals.
Related to the size, it can vary a lot too, from tiny labels that do not exceed 10mm to big ones about 10 cm or more. The same for shapes, that can be very different depending on the design from the client.
The manufacturing of customized RFID labels
When the customer order has been of customized RFID labels and it doesn’t of wet inlays or white wet inlays, anyways we have to produce wet inlays first. Always it is needed to manufacture wet inlays to produce customized RFID labels later. In addition, the frontal faces can be of very different materials.
Manufacturing steps
In the same converting machine where we have manufactured the wet inlays, we make a second process to add the frontal layer required for the customer, and to cut the customized shape of the label according to the client design.
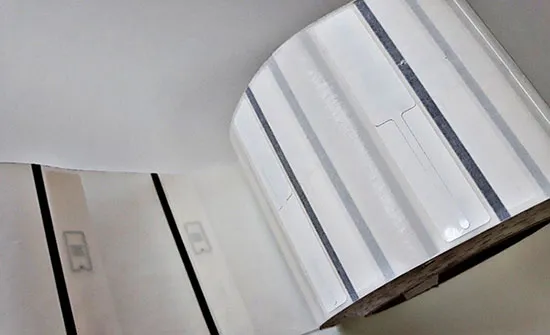
Materials that form an RFID label
The materials are very diverse, from papers to plastics, on the other hand, it will be avoided the use of metals because they affect the right working of radiofrequency. The only metals we find will be in the chip and the antenna.
The codification and printing
After the manufacturing of RFID labels they pass to the codification line, and some cases. also to the printing step. In Trace ID, we codify the labels by SATO machines, that also can print plain elements or barcodes.
Checking test
RFID tags go through various quality controls in relation to their performance, correct coding, etc. In Trace ID, we execute the quality control through measurement and test solutions of the Voyantic brand.
We hope that all this information will be useful for all those interested in RFID technology. If you want to continue expanding the topic, we recommend you to take a look at the rest of the magazine articles, and especially to the next part of this topic —Part two: RFID tags applications.
Contact us for more information focused on your needs. If you wish to receive information about RFID technology, subscribe to our magazine.